In the world of machining, it’s hard to ignore the iconic Bridgeport milling machine. Since World War II, every machinist has had some experience with this versatile knee-type vertical milling machine. In fact, many machinists speak of the Bridgeport in the same tone of reverence that they reserved for their first muscle car as a teenager.
It’s easy to see why Bridgeport is so beloved. These machines were once so popular that they became the de facto standard for all vertical manual milling machines, earning the nickname “Bridgeport” even if they were manufactured under a different brand name.
So, what makes the Bridgeport such a standout machine tool? Here are six things to know about Bridgeport machines that have set them apart from other manual mills:
Who Makes Bridgeport Mills Today?
Following its acquisition by the machine tool conglomerate Hardinge, Inc. in 2002, Bridgeport underwent some changes. Hardinge began producing different versions of the classic Bridgeport mill while continuing to manufacture the original Series I machine. However, the newer models produced by Hardinge are often CNC machines, meaning that they utilize program codes to drive the machine transmission.
Fast forward to today, and we have the V-Series, GX-Series, and XR-Series as the latest iterations of the Bridgeport milling machine. These modern machines come with an array of advanced features and are enclosed for added safety.

What Are The Main Parts Of A Bridgeport Mill?
Knee
The knee is a heavy-duty casting that supports the worktable, moving vertically on a dovetail on the machine’s column. This enables operators to adjust the table’s height manually using the vertical feed crank, allowing knee travel along the Z-axis. Once the knee is in the correct position, the operator can lock it.
Turret
The turret sits on top of the column and connects it with the ram, rotating as needed by loosening up a series of nuts. This enables the cutting head to access otherwise hard-to-reach areas on the worktable. Some mills come with a protractor marking on the turret, allowing precise positioning along the worktable.
Ram
The ram is locked into the dovetail assembly on top of the turret, enabling it to move in and out using a rack and pinion mechanism and a crank. A large hole on the back of the ram allows for mounting attachments. And because the ram is on a turret, the operator can swing the attachment 180 degrees and use it above the worktable.
Saddle
The saddle is responsible for supporting the worktable and is driven by a screw, moving in and out along the Y-axis on a dovetail alignment. Operators can move it manually using the cross-feed crank or with a power feed. Once the desired position is achieved, the saddle can be locked in place.
Worktable
The table sits on top of the saddle and moves horizontally along the X-axis, allowing for machining of workpieces. Operators can move the table manually using handwheels or engage the power feed if the machine has one. Locking levers minimize vibrations, and T-slots machined into the table’s surface aid in clamping workpieces or vises for machining.
Head
The head houses the spindle and the quill. The original Bridgeport mill has a C Head, but most come with a J Head. The spindle speed range varies depending on the head and motor attached to the machine. Operators can swivel the head 90 degrees left or right and 45 degrees up or down, with protractors on the tilt joints for precision.
Quill
The quill is a unique feature of the Bridgeport mill, allowing it to function as a drill press by moving the spindle up and down using the quill feed handle. Operators can move it manually or with an optional power quill feed. The quill travel is 5″, and the diameter is 3.375″. For boring operations, operators can raise and lower the quill slowly.

Hardinge Bridgeport V480
Spindle HP & Speed: 5.5 / 7.5 kW (Fanuc) (Contin./ 30 min) & 10,000 RPM Up to 12,000/15,000 RPM optionally (max):
Why is it Called a Bridgeport?
The Bridgeport Milling Machine, a type of machine and a brand name, originated from Bridgeport, Connecticut and was first sold in 1938. It gained popularity in the subsequent decades for its small to medium-sized vertical milling machines that featured a distinctive quill-equipped multiple-speed vertical milling head mounted on a ram-on-turret over a knee-and-column base.
According to the biography of Rudolph Bannow at the American Precision Museum, he envisioned this iconic design in 1936 as the ideal machine to mount the milling head already being produced by the Bridgeport Pattern and Model Works.
The success of Bridgeport’s manual milling machines has been so widespread that the term “Bridgeport” is now commonly used to refer to any vertical milling machine with the same configuration, regardless of the manufacturer. Several other companies have replicated this design.
Today, the Bridgeport brand still offers this configuration in both manual and computer numeric control (CNC) versions, although tool-changer-equipped machining centers are also a prominent part of the product line.
Applications of a Bridgeport Mill
In any machine shop, Bridgeport mills are known to be among the most versatile machines available. Thanks to their rotating turret, movable ram, Z-axis movement from the knee and quill, and tilting head, machinists can perform a wide range of tasks, including milling, facing, drilling, tapping, boring, reaming, and angle cuts.
Despite their relatively small footprint, Bridgeport mills are also renowned for their rigidity. Weighing in at only 2,000 pounds, machinists can take deep cuts in tough materials on these machines with ease. This is because Bridgeport mills are manufactured with a solid cast iron frame that boasts excellent vibration-damping qualities, allowing them to withstand the vibrations and impact of heavy cuts.
This level of rigidity means that Bridgeport milling machines can machine flat or irregularly shaped surfaces with larger face mills and cut gears or slots using smaller end mills. With a drill chuck or R8 collet in the spindle, these machines can drill, tap, bore, and ream quickly, particularly if they have a variable speed head. In fact, Bridgeport mills are so well-made that machinists can even broach keyways without fear of damaging the machine.
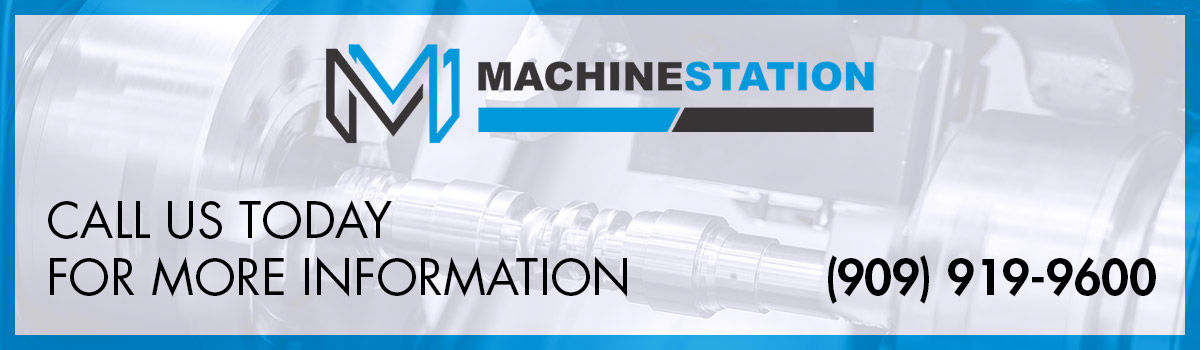
What is the Difference Between a Bridgeport Mill and Other Mills?
Milling machines are a critical tool for removing material from a workpiece by rotating a cutting tool and feeding it into the material. While several types of milling machines exist, knee-type and bed-type are the most common.
Despite the ability of both types to mill, drill, bore, and cut slots, the vertical knee mill is the favored option for its versatility, found in most machine shops. With this type of milling machine, the table mounts on a knee that moves vertically along the column, permitting up-and-down movement and easy workpiece position adjustment. Additionally, the milling head tilts for machining at various angles.
Conversely, bed-type milling machines have a fixed table and movable ram, making them more powerful than knee mills, with a bed mill carrying nearly double the load of the latter. The cutting tool mounts on a vertical or horizontal spindle that moves along the bed to remove material from the workpiece. Their stability is their advantage over lighter machines, enabling them to handle more massive workpieces.
Bed-type milling machines offer excellent stability and accuracy, thanks to their durable construction and the secure clamping of the workpiece to the bed. These machines come in various sizes and configurations, ranging from small benchtop models to large floor-standing machines.
To summarize, milling machines come in two types: knee-type and bed-type. While both types can perform similar tasks, knee-type milling machines are preferred for their versatility, while bed-type milling machines offer greater load capacity and stability. Bed-type milling machines also provide superior accuracy and precision due to their sturdy construction and secure workpiece clamping.